The construction of the steel cage is the significant part of the basic bridge construction.In the past of the traditional construction, reinforcement cage uses the manual rolling or the manual welding, except low efficiency,The main shortcoming is that the quality of the cage is poor and the equipment size is not standard which deeply affects the construction period and quality of project. The Steel Cage Welding Machine, Which combines steel straightening, bending forming with rolling welding, makes steel cage processing bacially realized mechanization and automation, reduces the process time and the deviation between various links, greatly improving the quality and efficiency of the steel cage forming, so as to creates a good economic and social benefits for the construction units and become the future development direction of reinforced cage.
Highlights
- It is of high automatic, fast processing speed . Compared with the ordinary manual molding, it is 3 ~ 4 times more than traditional manual production
- The processing quality is stable and reliable: with mechanical operations, the main reinforcement and the pitch of the winding is uniform and with high accuracy. Because of the mechanical rotation, the plate reinforcement works closely with the main bar wrapping. Adding stirrup after forming, the uniform diameter can ensure the concentricity of the reinforcement cage. The product quality meets the standard requirements completely. The supervision of mechanized processing of steel reinforcement cage basically implements the “exemption”.
- The processing cost is greatly reduced, when complete the same amount of work, mechanical production can save 3/4 of the manpower
- Workers fatigue strength is greatly reduced, due to the mechanical operation, workers play a supporting role. Construction image is greatly improved.
- Stirrup does not need overlapping, compared with the manual operation, it saves 1% of the materials, which reduces the construction cost. Due to the uniform distribution of main bar in its circumference, it is very convenient when more than one of steel cage overlaping and saves installation time
Model | KZ1500X | KZ2000X | KZ2500X |
Cage diameter (mm) | φ500-1360 | φ500-1860 | φ500-2360 |
Cage length (m) | 2-12 | 2-12 | 2-12 |
Max weight of reinforcement cages (KG) | ≤4500 | ≤6000 | ≤8000 |
Diameter of main bar (mm) | φ16-32 | φ16-32 | φ16-32 |
Spiral diameter (mm) | φ6-12 | φ6-12 | φ6-12 |
Spiral spacing (mm) | 50-500 | 50-500 | 50-500 |
Labeled electric power (kw) | 18 | 21 | 25 |
Walking speed (m/min) | 1.1 | 1.1 | 1.1 |
Rotating speed (r/min) | 2-3 | 2-3 | 2-3 |
Over 0imension (L*W*H)(mm) | 27,000x4500x2700 | 27,000x5000x3200 | 27,000x5500x3700 |
Feeding → inserting main bar → fixing →overlaping spiral→ welding → normal welding→ stop welding → cutting spiral → Separate fixed disk → loose tendons →separating movable disk → unloading cage→ lowering electric support → homing movable disk
technical solutions
1.Staffing
Under normal circumstances, 5 to 6 person can work.Specific distribution is as follows:
Preparation and feeding materials:2 people
Roll welding:1~2people
strengthening hoop: 2people
The Specific number of peope should be based on the size and the model of the steel cage.
2.Production efficiency
1500mm pile cage: two classes, can processe 300-400 meters / stand (about 20 tons) one day.
When Welding a 12-metre steel cage, the general loading and unloading time is approximately 15-20 minutes, normal welding time is approximately 18-25 minutes (spaced 120), so tne conprehensive time is 30-45 minutes, the speed can be greatly improved after skilled.(generally,the weight of a steel cage with diameter of 1.5 meters and length of 12 meters is about 800 kg)
The efficiency of forming steel cage is related to the number of the main bars, the diameter of the reinforcement, the pitch of the wound and the operation of the workers.
3.Steel cage template
With different project, the design of reinforcement cage will be changed (such as the number or diameter of main reinforcement ), it can adapt to different engineering needs by changing the template and the catheter.
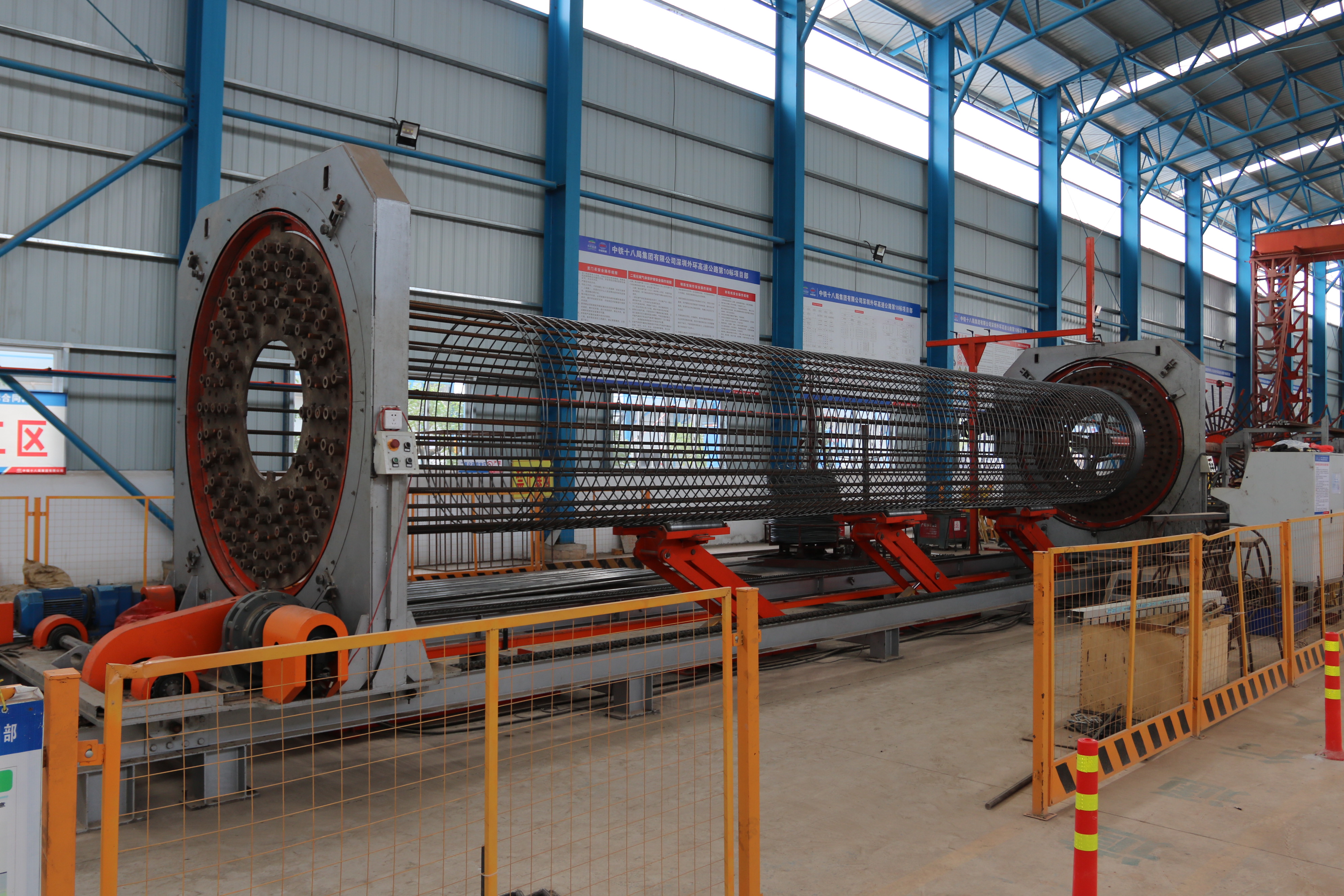
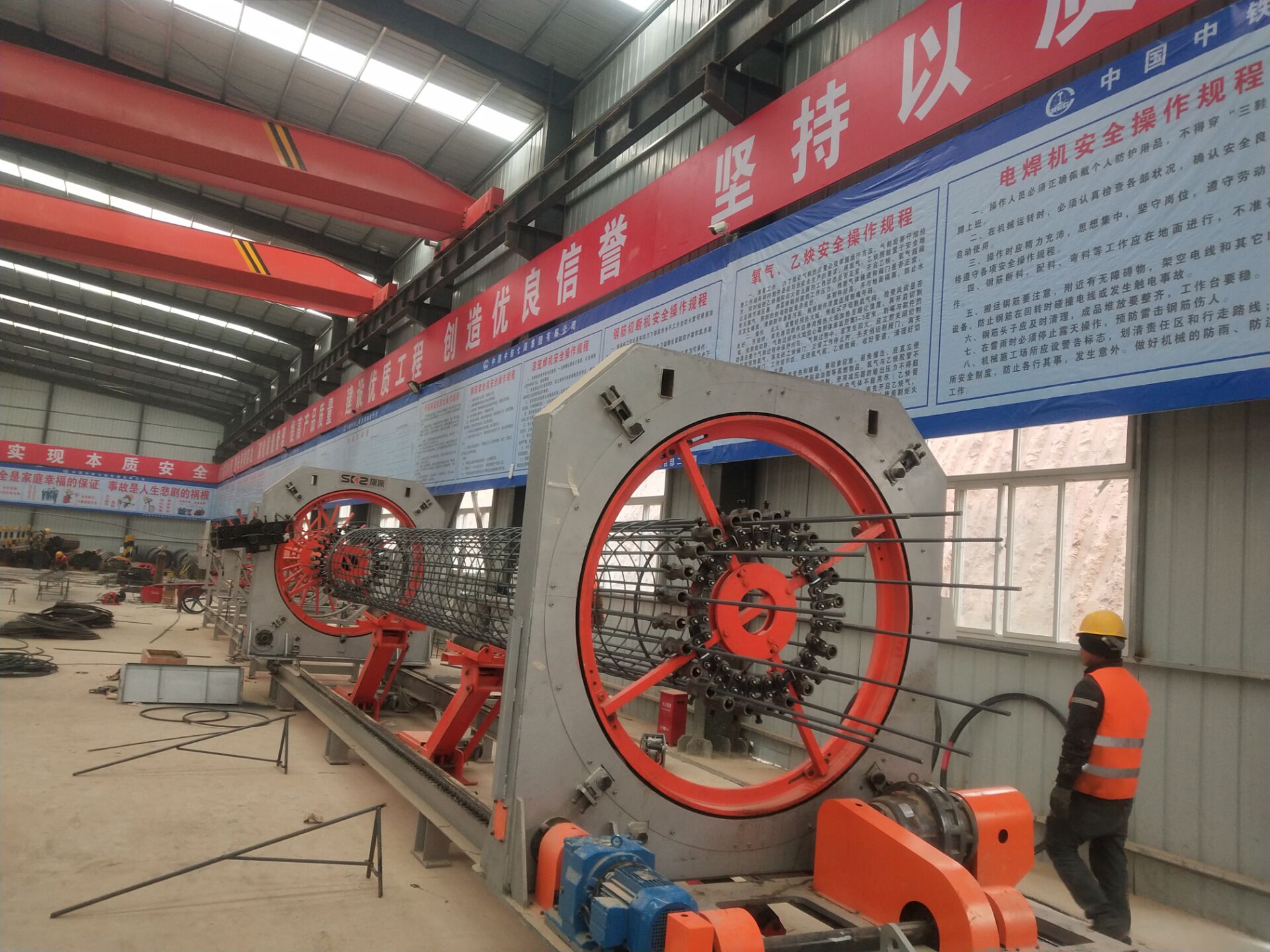
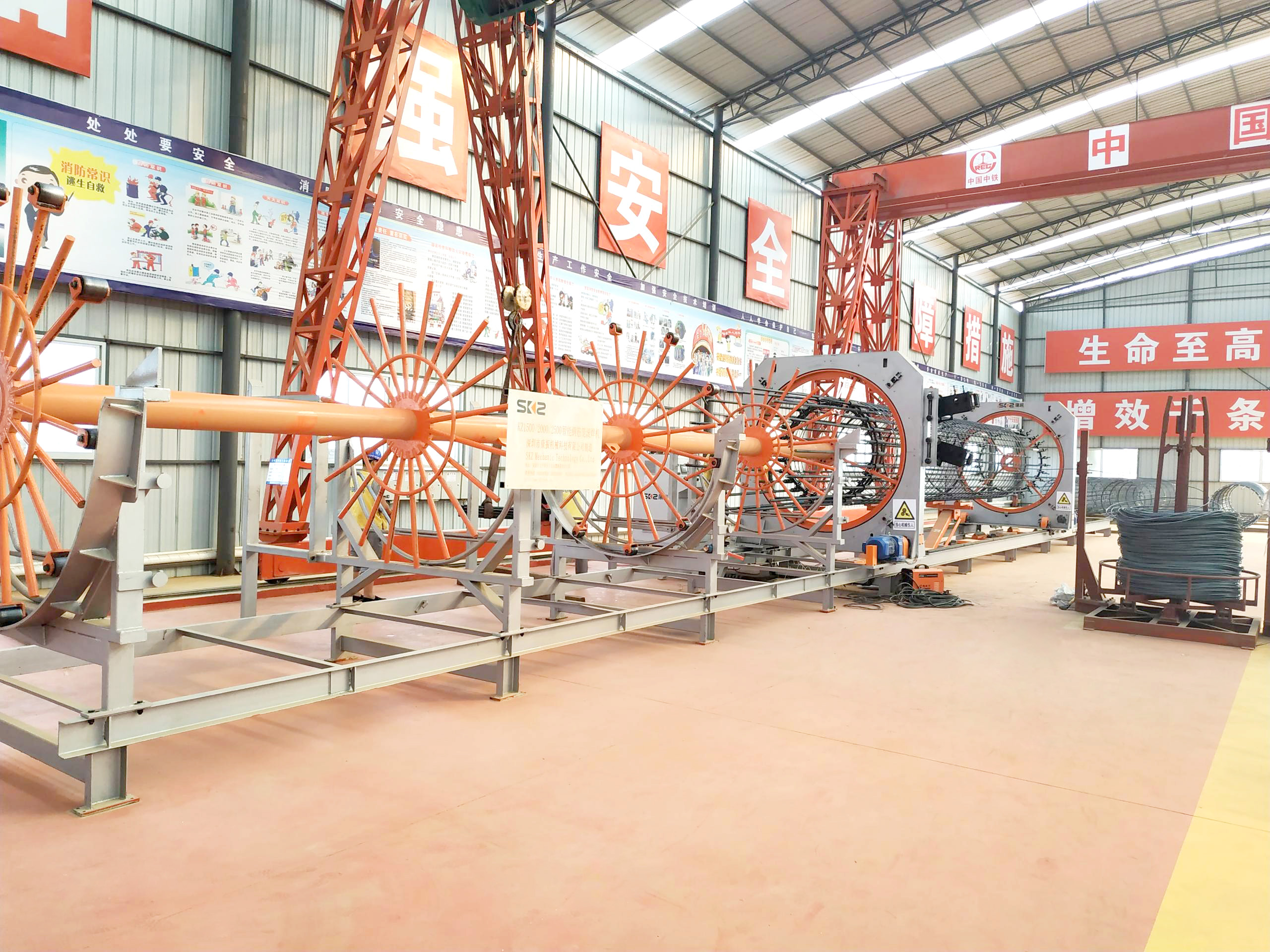
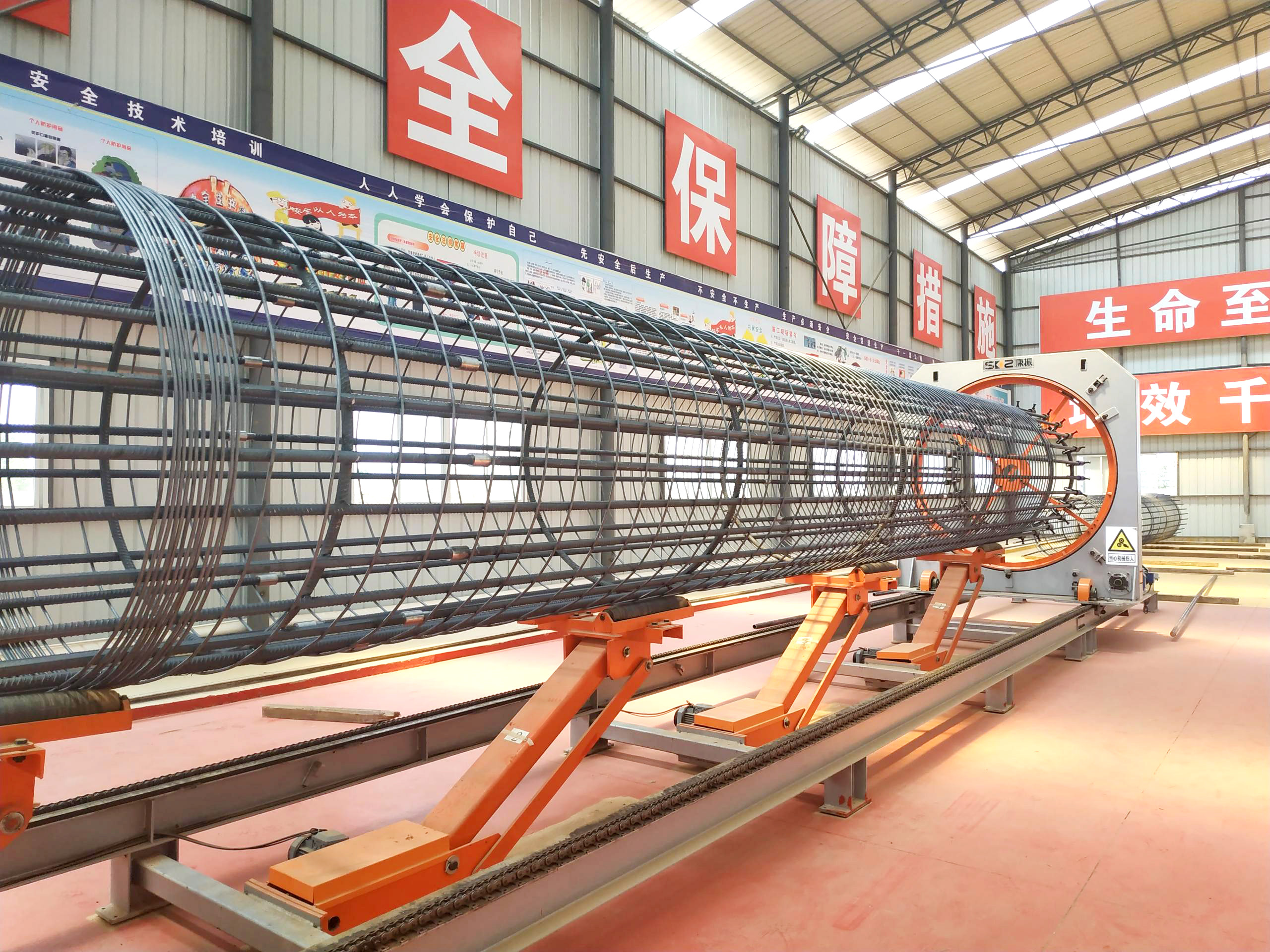
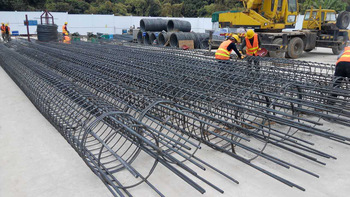